Improve the way you organize your company's facilities maintenance data
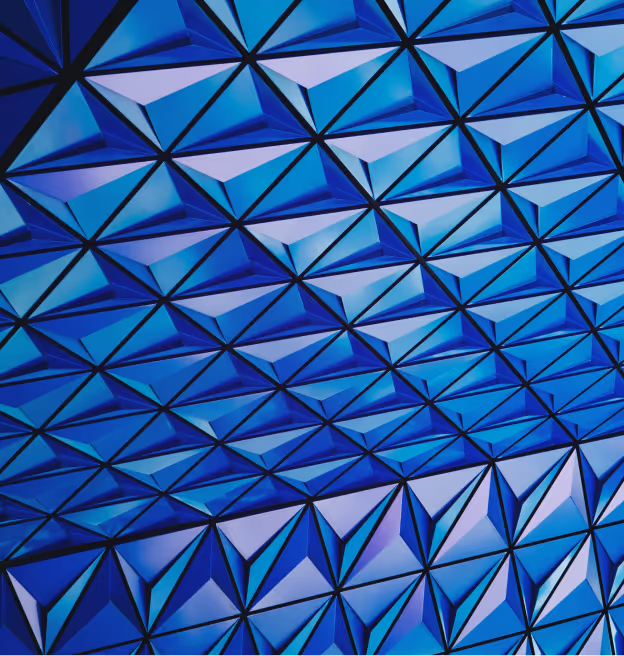
Surprisingly, the typical R&M operation includes a large amount of data. Simple data, (e.g. vendor names) and rich data (e.g. work order details and pricing) can be equally challenging to organize. When managing thousands of locations, it only gets harder to use data to scale up and manage effectively.
So, where should we start? Well, effective data utilization begins in the overlooked task of recording your FM results in an organized and actionable way. If you can’t find your vendor information because their data is scattered and titled incorrectly (e.g. ACME, ACME Co, ACME Inc., or ACME Incorporated) your company may be susceptible to a considerable amount of wasted time, extraneous effort and errors. In addition to keeping your data organized, it is important to collect data that is helpful when evaluating and conducting root-cause analyses. Data that is actionable will support long-term trends and provide useful insights you can act on.
By incorporating the following tips into your strategy, your company can have instant access to clean and organized information without breaking a sweat:
1. Standardize the Way You’re Collecting FM Details
Setting guidelines as you record FM data could be the difference between reviewing data that is reliable or invalid. For example, without an abiding process, a company may look back at last year’s lighting records and see inconsistent entries from past services. In some stores, the lighting records might only show the initial problem reported (e.g. the lights in the bathroom won’t turn on) without noting what caused the lighting problem. In other stores, the team may capture full work order details (e.g. a circuit board blew due to the HVAC overheating and the lights in the bathrooms were out because they were hooked up to the same circuit) but fail to document how they solved the request. Missing details of a maintenance request can lead to data inconsistencies and eventually company losses.
Creating a data entry process for vendors and employees will guarantee that all work orders will be in the same format with similar details so it is easy to refer back to when you need it. Ensuring everyone has the same method for recording all the necessary details of the services can also create better habits and eliminate many process errors.
2. Organize Your FM Data So it is Useful To Your Company
After creating a process, it is essential to clean your data and keep it useful. The way you filter your data can affect the accuracy of your information and influence the business decisions you make. Here are a few options to ensure your decisions are backed by valid data:
- Vendor tracking is a useful practice for nationwide companies that rely on multiple vendors throughout the country. Keeping track of how long it takes every vendor to complete a request allows for the monitoring and comparing of maintenance histories. Companies can also minimize the time vendors spend per service and ensure vendors get their work done in a single visit when possible by setting up a rating system where store managers give feedback of each service.
- Tracking each facility makes it easy to identify a location that has a history of expensive maintenance issues or trends such as aging buildings, equipment and grounds. These problems can be extremely difficult to keep safe and functional, and if a company realizes a trend of issues, they can take their historical data to make the best choice for their business and bottom line moving forward.
- Asset tracking management allows a company to use strategic decision making when maintenance issues arise within their facilities. Historical repairs can help a company decide if it would be best to replace the unit or repair the issue. For most companies, two to four percent of work is performed on assets under a warranty. By tracking asset warranties, companies can save on their maintenance costs.
- Monitoring by the problem provides recognition on what is causing the most issues within a facility. With this additional insight, companies can put plans into action, such as preventative maintenance to stop R&M problems from occurring as much.
3. Interact with Your FM Data Daily
Once companies have their data organized, they realize how difficult it is to take full advantage of their data. Their team might get too busy with a new project to continue working with data.
It can be extremely helpful to create a team of employees that are specifically responsible for contacting vendors for maintenance requests. These employees can devote all their time to using the data to dispatch contractors who arrive on time, complete repairs quickly, and follow the set standards. It is also possible for these employees to track spend when managing work orders to ensure consistency. Your company won’t have to suffer from gaps in your data because they will continuously update your information as new requests and services arise.
If you are interested in additional information regarding the way your company can use your data, stay on the lookout for the next blog in our data series by subscribing to our blog, here.
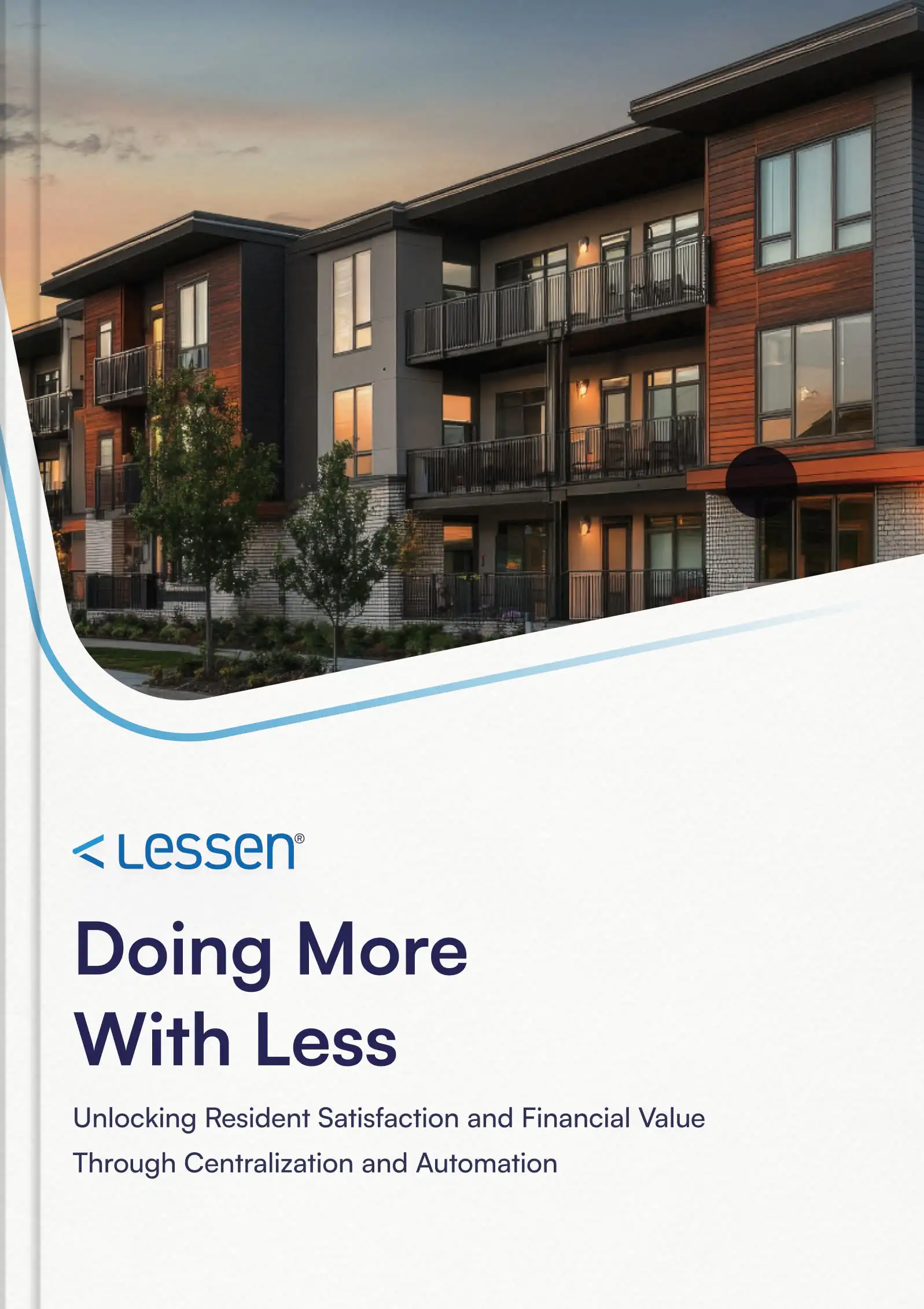
- This is my list