Meet Robert Martin, VP of Hard Services
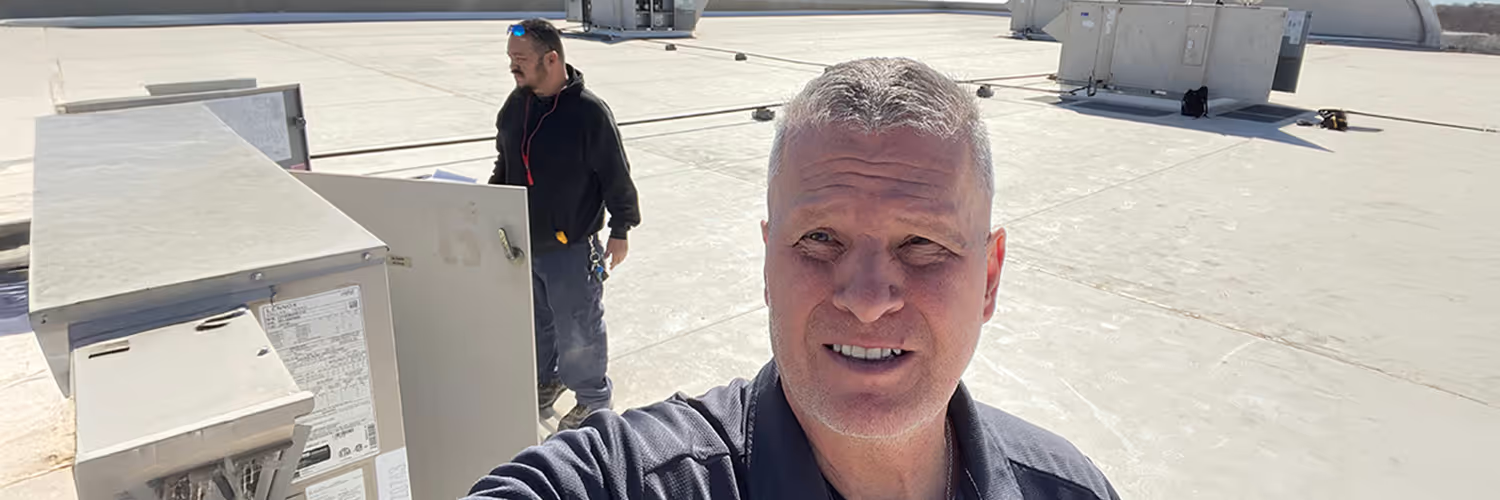
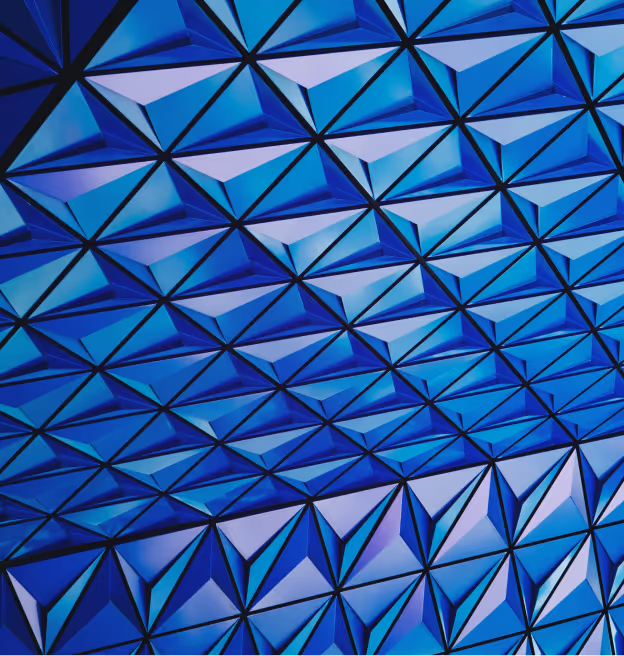
Robert Martin is the Vice President of Hard Services for Lessen.
What is your role at Lessen?
What I do is education. Many of our customers didn’t come up from the facility management world, so they don’t have hands-on mechanical experience. I try to teach them about their facilities. And I don’t just teach remotely. I travel to their facilities so they can learn about their properties first-hand to help them understand all the little details that, for example, can affect the heating and cooling system.
One of our customers is a major pet retailer. By visiting one of their sites, I found that the reason their HVAC equipment was faulty was because they had hair clogging all the vents. And the vents had never been cleaned. Which meant they were getting maybe 12 years out of their equipment instead of 18 years. They only discovered that because I showed up and did the inspection myself.
What they learned is that if you manage the environment better inside the building, you’ll get equipment that lasts longer and is more efficient.
What are the benefits of a preventative maintenance protection program?
A preventative maintenance protection program almost acts like an insurance policy on units less than 12 years old. You pay a certain amount per year, and we cover all the repair and replacement costs of your assets, the labor costs, the service calls – You get that at a single price. Essentially it guarantees you won’t have any problems and if you do, we cover it. You’re not spending on reactive costs, which means you can repurpose that money into your capital plan.
Does being on-site make you unique?
Yes. Anyone can pull up a preventative management checklist and give it to a technician. But sometimes those technicians only have an hour to get the job done, or they are specialists in one area but don’t have a thorough understanding of all the issues that affect a facility. To do a thorough inspection, and to discover things that are impacting the facility today and will impact it years from now, you need on-site time, and you need expertise.
I’m a different breed. I want to understand the customer’s facilities better than they do. If you can’t understand the issues that are increasing your work orders at a site level, you won’t understand the issues across your entire facility portfolio.
What is the most important thing commercial property owners should know?
You need to invest in your assets in advance of them failing. For example, I went into the corporate office of one of our customers and asked the vice president of facilities what kind of capital program they had. He said they didn’t have one. He said if a piece of equipment fails, they’ll replace it. Or if one of their facilities wears down completely, they’ll just build a new one. That isn’t a strategy. Our job is to show them how a strategy will not just extend the life of their facilities, it will save them money and time over the long term.
You must have a preventative plan. You also need a long-term strategic project plan. Because everything has a useful life. The key is maintenance. To get 30 years of life from an electrical panel, you must clean it every two years, for example. A capital plan is a big part of that preventative approach.
What do you like most about your role?
I like solving problems. I draw from more than 35 years of experience. I want to be a problem solver for customers. I enjoy being on site and telling our customers the good, the bad, and the ugly about the state of their sites. No one else is going to tell them. I like being on site and conducting and inspection before we have those kinds of conversations.
What did you do before you came to Lessen?
I served in the US Navy as a chief petty officer. I was taught by the best engineers in the propulsion plant engineering department aboard three different aircraft carriers. We had to have a solid preventative maintenance program because it was costly to replace broken parts, and an aircraft carrier cannot fulfill its mission if the ship is dead in the water. Our preventative maintenance program was inspected constantly. That’s how stringent it was. We had maintenance requirement cards which gave you step-by-step instructions and the inspector knew if you were going by the cards or not.
After the Navy, I worked in similar roles at places like the American Airlines M&E Base in Ft Worth, Texas, Menasco Aerospace, ServiceMaster Business and Industry Group, Aramark B&I Group, Starbucks, and with Siemens Enterprise Division, where I utilized my energy and facility management background to help these organizations gain maximum benefits out of their EMS platforms as well as extend the useful life of their capital assets.
I’ve been a disciplined person all my life, and my passion for facilities management drives me to do the best for our customers every day.
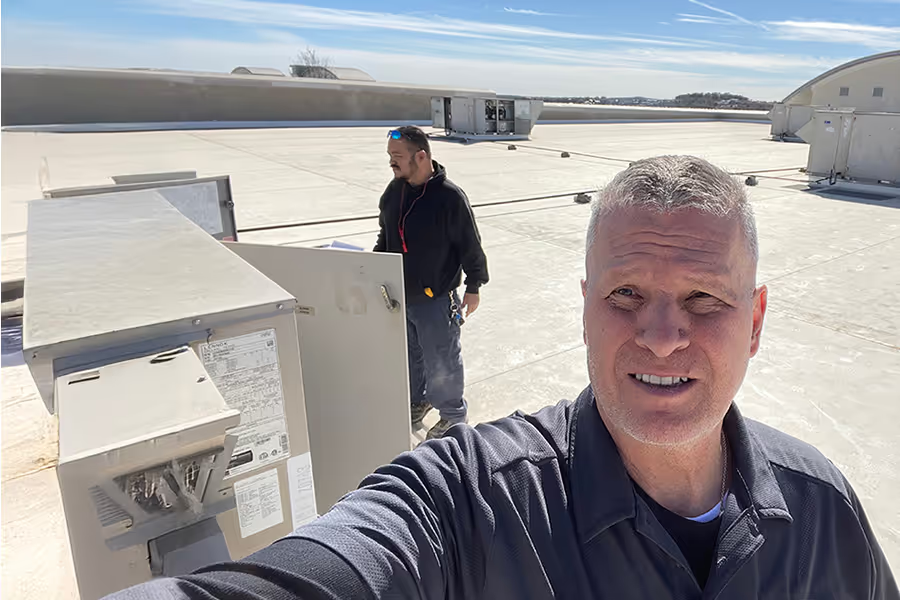
- This is my list